Qantas Engineers Boost On-Time Flights
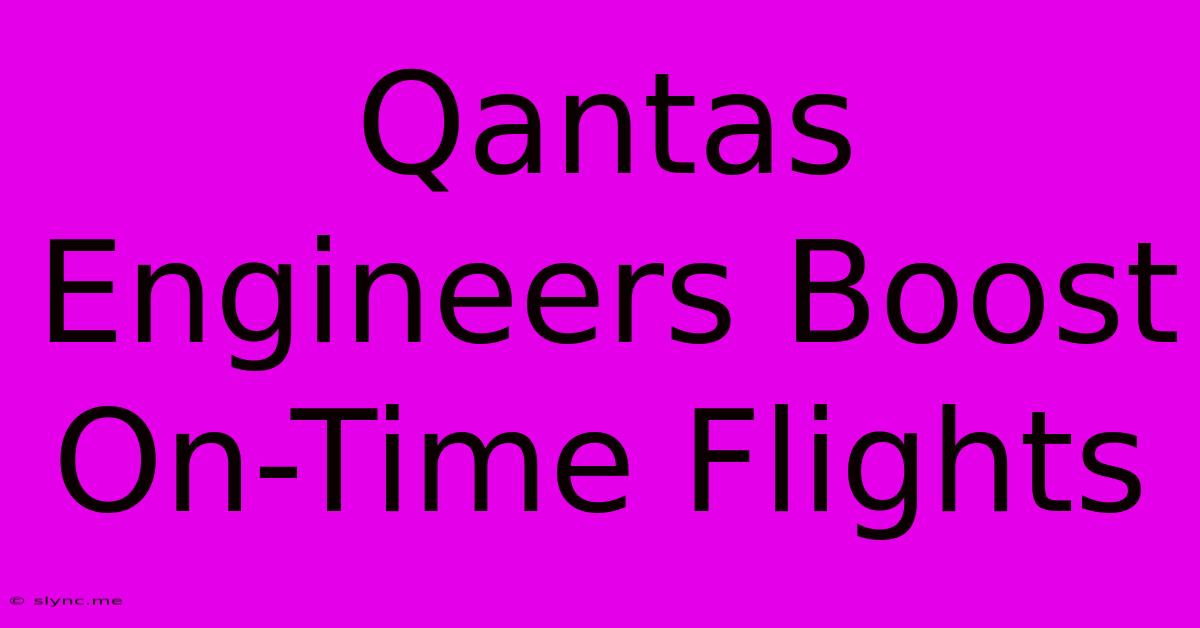
Discover more detailed and exciting information on our website. Click the link below to start your adventure: Visit Best Website Mrs.Amykhan. Don't miss out!
Table of Contents
Qantas Engineers Boost On-Time Flights: A Deep Dive into Maintenance Excellence
Qantas, Australia's flagship airline, has long been renowned for its reliability and on-time performance. Behind the scenes, a dedicated team of engineers plays a crucial role in ensuring smooth operations and minimizing flight delays. Recent initiatives and advancements in maintenance strategies have significantly boosted Qantas' on-time flight record, leading to increased passenger satisfaction and operational efficiency. This article delves into the key factors contributing to this success.
The Impact of Proactive Maintenance
One of the most significant factors contributing to improved on-time performance is Qantas' commitment to proactive maintenance. Instead of relying solely on reactive repairs after problems occur, the airline employs a sophisticated predictive maintenance program. This involves leveraging advanced data analytics and sophisticated diagnostic tools to identify potential issues before they escalate into major problems that could ground aircraft.
Data-Driven Decisions: The Key to Success
This data-driven approach uses real-time data from aircraft sensors, historical maintenance records, and even weather forecasts to anticipate potential mechanical failures. This allows engineers to schedule maintenance during less critical periods, minimizing disruption to flight schedules. The system constantly learns and adapts, becoming more accurate in predicting potential problems over time.
Investing in Advanced Technology
Qantas has invested heavily in advanced technologies, including specialized software and diagnostic equipment. This allows for faster and more accurate fault diagnosis, reducing the time spent troubleshooting and repairing aircraft. The use of augmented reality (AR) technology is also enhancing the efficiency of maintenance procedures, guiding engineers through complex repairs with greater precision and speed.
Streamlining the Maintenance Process
Beyond proactive maintenance, Qantas has also focused on streamlining its overall maintenance processes. This includes:
Optimized Workflow and Training
Improved workflows and highly skilled technicians contribute to faster turnaround times between flights. Rigorous training programs ensure engineers possess the expertise to handle a wide range of maintenance tasks efficiently and effectively. Continuous professional development keeps their skills sharp and up-to-date with the latest technological advancements.
Enhanced Parts Management
Efficient parts management is crucial for minimizing delays. Qantas has implemented a robust inventory system, ensuring the necessary parts are readily available when needed. This minimizes downtime waiting for crucial components, contributing to a faster turnaround time and fewer delays.
The Results: Improved On-Time Performance & Passenger Satisfaction
The combined effect of proactive maintenance, streamlined processes, and technological advancements has resulted in a noticeable improvement in Qantas' on-time performance. This translates directly into increased passenger satisfaction, as fewer delays mean less stress and more reliable travel experiences. The airline's reputation for reliability is further strengthened, attracting more passengers and contributing to overall business success.
Conclusion: A Culture of Excellence
The success of Qantas' improved on-time performance isn't just about technology; it's about a culture of excellence that prioritizes proactive maintenance, continuous improvement, and a highly skilled workforce. This commitment to operational efficiency not only benefits the airline but also enhances the travel experience for millions of passengers each year. The ongoing investment in technology and training ensures Qantas will continue to lead the way in aviation maintenance and on-time performance.
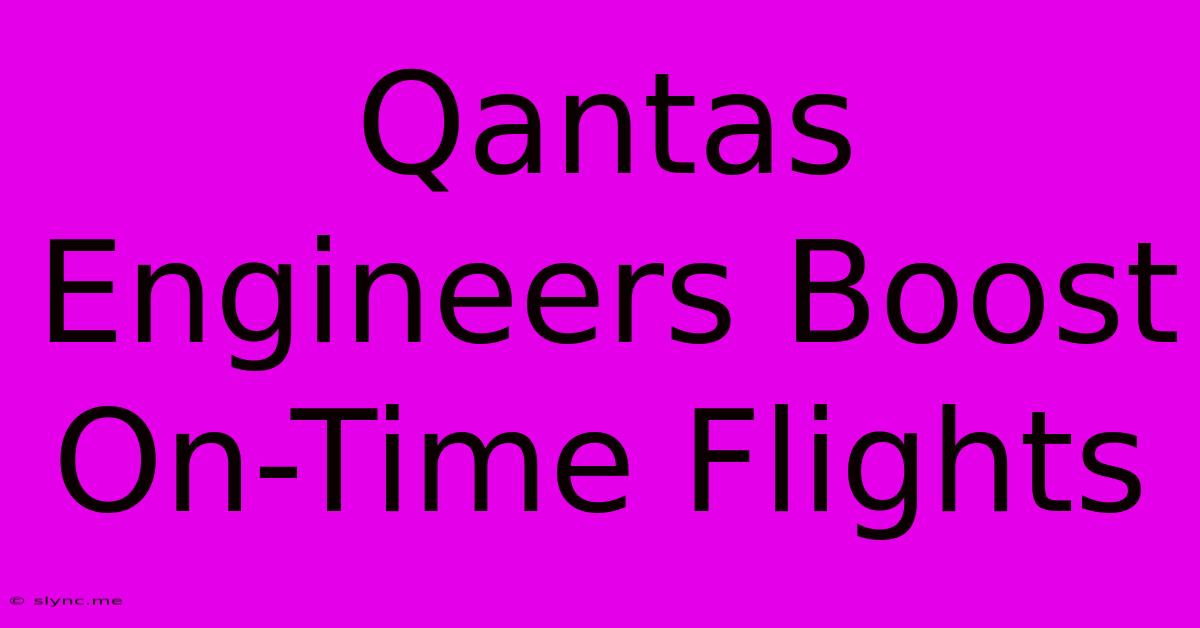
Thank you for visiting our website wich cover about Qantas Engineers Boost On-Time Flights. We hope the information provided has been useful to you. Feel free to contact us if you have any questions or need further assistance. See you next time and dont miss to bookmark.
Also read the following articles
Article Title | Date |
---|---|
Man Utd Man City Team Updates | Dec 13, 2024 |
Witcher 4 Next Rpg From Cd Projekt Red | Dec 13, 2024 |
Bezdoganna Gra Ukrayinets U Lizi Chempioniv | Dec 13, 2024 |
Emotional Retirement For Beloved Star | Dec 13, 2024 |
Nul Propuschenikh Ukrayinets Bliskuchiy U Lizi Chempioniv | Dec 13, 2024 |